EXPERTISE
Medical Device Process Validation
Medical Device Process Validation is Crucial for Your Success
Optimize your medical device process validation strategy by leveraging QA Consulting’s quality assurance and regulatory expertise.
To get your medical devices to market—and keep them in use—you need effective medical device process validation. Regulatory agencies require it and patients and health care providers rely on it. Process validation for medical devices involves creating a plan to monitor and refine manufacturing procedures. A well prepared plan ensures products are safe and meet specified user, technical, and regulatory requirements.
While essential, optimized process validation strategies can be difficult to define, implement, and maintain. Without reliable process validation, manufacturers risk incurring costly production delays and time-consuming regulatory scrutiny. QA Consulting has the expertise to help you design, implement, and maintain a medical device process validation strategy that keeps your production lines moving.
Are you ready to validate your process with an expert?
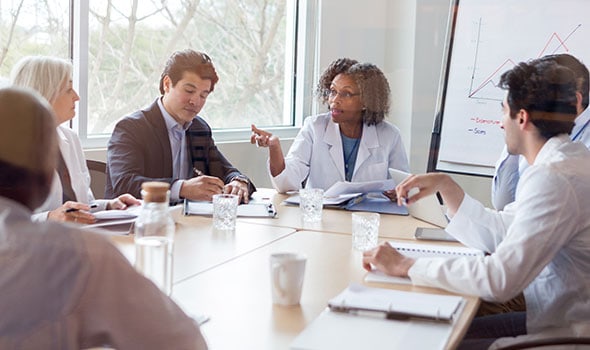
Why is validation necessary for medical devices?
Validation ensures safety.
Medical devices directly impact the lives and health of countless people. The components, assembly, and installation of these devices need to be assessed for quality, consistency, and precise performance under standard operating conditions. The safety and performance of medical devices are vital for patients.
Validation ensures effectiveness.
Virtually all aspects of the patient care continuum employ medical devices. They play a vital role in everything from diagnosis to treatment to monitoring. Validation of medical device processes assures their consistency, efficiency, and effectiveness in patient care and treatment. Validation also assesses the cost-effectiveness of a given product. All of these measures promote the success of medical devices in clinical practice.
Validation ensures regulatory compliance.
FDA and ISO 13485 regulations exist to ensure the safest and most effective patient outcomes from medical devices. In an ideal world, someone would test and verify every device produced. However, the cost and logistics involved make this impractical. As a result, medical device process validation fulfills this critical quality assurance requirement.
Without proper validation and regulatory adherence, businesses and their products are vulnerable to failures in the marketplace and regulatory actions by governing bodies. Poor product performance and the imposition of regulatory restrictions both tarnish a company’s reputation and require costly remediation. If validation is not done, or done poorly, FDA inspectors issue a Form 483 that outlines the issues and requires timely correction. Receipt of a FDA Form 483 can be particularly disruptive and expensive, especially if major changes are necessary to retrospectively validate a device or device manufacturing process.
Production costs will then escalate to deal with increased testing, inspections, reworking, and material costs. In the event of product-related injury or harm, grounds for litigation will be firmly established. The QA Consulting team is here to help you avoid or recover from these circumstances.
How is a successful process validation program designed and implemented?
When a manufacturer has a functional design and manufacturing infrastructure sufficient to complete the validation process, it is important to initiate a validation program.
First a process Validation Master Plan (PVMP) should be established to define the processes that require validation.
Then you’ll need to develop appropriate quality assurance protocols for each stage of the manufacturing process, such as sterilization and packaging.
- Installation qualification: IQ establishes confidence that process equipment and ancillary systems are capable of consistently operating within required limits and tolerances.
- Operational qualification: OQ challenges process parameters to assure they produce a product that meets requirements under all anticipated conditions of manufacturing.
- Performance qualification: PQ demonstrates that the particular process will consistently produce acceptable product under normal operating conditions.
From here, on-going process controls are determined to monitor and control the process. Manufacturers complete ongoing documentation, review, and optimize processes before submitting process validation results to pass regulatory audits and internal inspections.
Medical device process validation employs a quality management system that examines the essential processes in the device’s manufacture by checking, testing, and recording outcomes.
What are the benefits of expert medical device validation services?
Save time by outsourcing time-consuming tasks
Medical device validation requires hours of work and a sharp eye for detail. By outsourcing to an experienced expert, you can save time and focus on your innovation. QA consulting experts will reliably conduct validation, while you concentrate on your core business.
Optimize your validation and operate with confidence
Knowing your devices and processes are validated gives you the confidence to proceed with your business plan: on time and on budget. QA consulting experts will help you design and implement optimized process validation that ensures seamless production of medical devices.
Remain audit and inspection-ready
Regulatory agencies will want to know you’ve met your obligations to them. Our experts in validation anticipate and comply with the regulatory requirements you need for superior audit and inspection reviews. Additionally, QA consulting experts can help your validation measures and compliance documentation satisfy all pertinent regulations.
Mitigate risks to keep manufacturing workflows on track
By working with an expert you can avoid validation roadblocks, such as cybersecurity threats and FDA inspection uncertainty. QA consulting is prepared to anticipate and prepare for these and other emerging challenges. Our wide breadth of medical device industry knowledge allows us to steer our clients through any potential issues that threaten manufacturing workflows and business as usual.
How can QA Consulting help?
Since every device or manufacturing process is different, it’s vital to have the capabilities and expertise to navigate the validation process. QA Consulting offers medical device manufacturers a custom-tailored approach to shepherd innovative products through validation and compliance.
- Medical device design and process validation
- Equipment deployment and qualification (IQ,OQ, PQ)
- Medical device manufacturing validation
- Automation system validation
- Chemical and purification process validation
- Medical device software validation
- Cleaning validation
- Sterilization validation
- Validation training for employees
- Regulatory Compliance and Audit Inspection/Assistance (FDA and ISO 13485)
Our expertise helps clients successfully navigate complex regulatory and quality environments. As an extension of our client teams, we customize solutions to meet each client’s goals and needs. We’re not just an advisor. We’re a partner who will help you through your most challenging issues to achieve success.
QA Consulting, Inc. was instrumental in bringing CryoLife’s mechanical heart valves to market. Their expertise directly related to our devices enabled them to hit the ground running without extending our project timeline. They helped us reduce the engineering time needed and shortened our timeline for FDA approval. The quality and regulatory expertise of the QA Consulting team is unparalleled.
-Jeff Stark, Principal Process Engineer, CryoLife
Are you in need of a Medical Device Quality Assurance Expert?