EXPERTISE
Medical Device Quality Management System (QMS)
QMS for medical device manufacturing: tick all the boxes while ensuring success.
Creating a robust Quality Management System (QMS) is a complex, necessary process that can quickly become overwhelming.
However, you don’t have to do it alone.
We design Quality Management Systems for medical devices tailored to your company’s needs, providing step-by-step guidance to meet all regulatory requirements.
Let us do the heavy work.
Expert Insights
- Get started on your QMS and have it complete and operational prior to submission of your premarket notification (510(k)) or premarket approval (PMA). Once you complete your feasibility and proof of concept stages, it is an ideal time to start building your QMS in the design and development phase.
- Customize the QMS to your specific needs using a risk-based system.
- Don’t overcomplicate the QMS, but be sure to meet the regulatory requirements of the market(s) you want to enter.
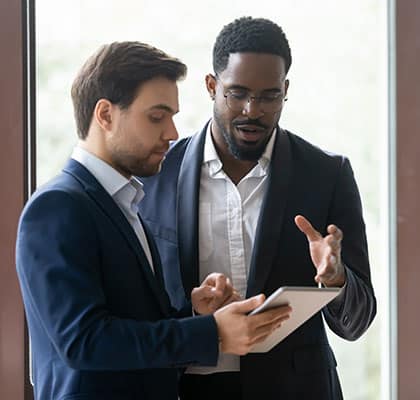
Developing a QMS: Pave Your Road to Success
A medical device quality management system (QMS) is a structured collection of processes and policies designed to cover all aspects of your product lifecycle, from its introduction to its growth, maturity, and decline.
By ensuring that your device meets customer expectations and regulatory requirements, a well-thought-out QMS can improve your organization’s performance and reputation. The right QMS helps your company, your employees, and your customers.
A few benefits of an effective QMS:
- Improve risk identification and management
- Simplify processes and traceability
- Reduce costs and delays
- Market your business more effectively
QMS complexity and costs are determined by your medical device’s risk-based classification and target market. Failure to meet regulatory requirements can result in development and distribution delays, fines, or a complete shutdown by the authorities.
QA Consulting develops custom-tailored, robust quality management systems that ensure product safety and a 100% success rate in FDA inspections and notified body audits. Our team are experts in quality systems, microbiology and multi-national regulations, and will help you commercialize your medical device effectively.
Implementing a QMS: Get Everyone on Board
QMS implementation without a proper understanding of its challenges threatens compliance. This may delay your medical device’s production, registration, and distribution.
Major changes in a company’s framework can lead to misunderstandings and confusion for employees performing crucial tasks. It is essential that your team members benefit from appropriate support and resources to ensure a smooth transition to the new framework.
Our specialists offer assistance in implementing the QMS that best suits your company’s expectations. We provide your staff with easy-to-navigate information and guide you step-by-step.
Here are some expert tips for implementing a QMS from Anne Holland:
- Staff at all levels need to understand how they contribute to and benefit from the QMS. Training and effectiveness verification is a must.
- Use of an eQMS is not mandatory, but improves both efficiency and accuracy. There are many shapes and sizes of eQMS systems so match the system to your company size and needs.
- When starting your QMS, I recommend implementing your QMS in a stepwise fashion. Start with the procedures needed for design control, document control, record control, purchasing/ supplier controls and management controls. From there, continue with the next phases of production and process controls: infrastructure, acceptance controls, complaints and corrective and preventive action (CAPA’s), etc.
Successful QMS implementation sets the foundation to manage growth more effectively, increase your medical device’s consistency and safety, and improve overall regulatory compliance.
Let us set your QMS implementation on easy mode.
Maintaining a QMS: Keep Your System on Track
Regulatory environments are constantly revised, causing existing procedures to quickly become obsolete and incomplete. To safeguard the quality of your products and your company’s reputation, an effective QMS requires regular updates and upgrades.
Here are two key expert insights for maintaining a QMS:
- Early Standards Operation Procedures (SOPs) implementation and comprehensive documentation are fundamental in tracking and maintaining medical device quality management systems throughout changes in regulatory guidelines.Robust SOPs are mandatory for the registration of a product and its commercialization on the global market. As the backbone of a successful QMS, SOPs ensure consistency and reproducibility in the production process, and help facilitate compliance with evolving quality and design changes for medical device manufacturers.
Become familiar with SOPs - Medical device document control is essential for a QMS to be effective and sustainable in the long term.
By tracking changes, revisions, and approvals, these documents provide evidence that you adhere strictly to company policy and are in compliance with up-to-date regulatory requirements.
Learn more about medical device document control
Our team of experts will help you to develop SOPs specific to your needs, improve your medical device documentation, and maintain your QMS in compliance with ever-changing domestic and international medical device regulations.
Let us keep your QMS on track.
Regulations and Standards Governing a Medical Device QMS
Regulatory requirements are determined by medical device classifications and your target market. For commercialization to be successful, an effective regulatory strategy and an in-depth understanding of the latest guidelines are crucial.
Key expert insights for EU Standards for a QMS:
Compliance with European regulatory requirements begins with ISO 13485.
ISO 13485 is specifically designed to support manufacturers in establishing a reliable QMS and ensuring a medical devices’ safety and consistency throughout their lifecycle. Manufacturers also must comply with the EU Medical Device Regulation (MDR) to obtain the CE marking needed to distribute their products on the European market.
Gain insight into EU MDR requirements
Key expert insights for US Standards for a QMS:
On the US market, medical device approval is strictly regulated by the Federal Drug Administration (FDA).
In accordance with the FDA quality system regulations (QSR) outlined in 21 CFR Part 820, medical device manufacturers are required to develop extensive SOPs to ensure reproducibility and consistency in the production process.
Learn more about FDA regulations
As experts in compliance and medical device quality management systems, our team will assist you through the implementation of regulatory requirements and best practices specific to your company’s needs. Create and follow a strong, personalized regulatory strategy and enter the regional or global market with confidence.
We will set your product up for success. Get a sneak peek into your future partners.
The Value of Partnering with QA Consulting
As global regulatory requirements become more stringent, with little to no room for error, ensuring the compliance of your medical device becomes harder and more stressful.
Outsourcing to QMS specialists ensures success to meet regulatory authorities’ expectations, and significantly bolsters development productivity and cost-efficiency.
Why QA Consulting?
As an ISO 13485-certified company, we have a deep understanding of the internal processes that regulate medical device quality management systems. With more than 100 years of combined experience and approximately 350 successful partnerships with medical device manufacturers, we excel at simplifying complex, time-consuming regulatory tasks.
As quality assurance, regulatory affairs, and microbiology experts, our team creates customized compliant solutions that meet your business’ goals and ensure the safety of your medical devices.
When you partner with QA Consulting, you gain access to a team of professionals that expand and sharpen their range of skills and industry expertise. The QA bonus? Reach out anytime for advice on new projects or to follow up on our previous collaborations.